Incoming Quality Assurance Parameters Recommended for Water Labs
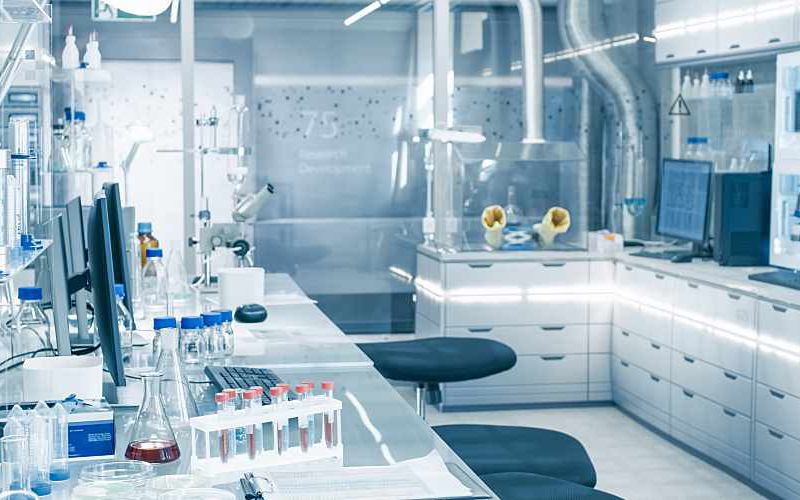
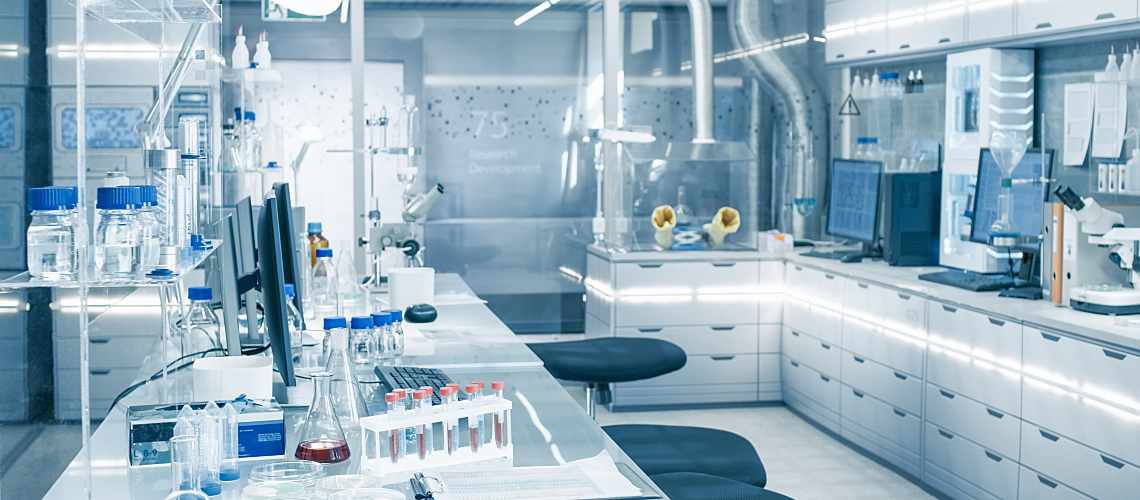
Imagine this: Your water testing lab has a huge contract on the line to analyze a volume of samples. The timeline is tight, and your performance will determine the future of this key business relationship. Halfway in the process, you discover an expired reagent was used in testing. You now have to throw out your results, notify the client of the delay, and wait for the replacement reagent — that's assuming you appropriately stored enough sample volume to retest.
An incoming quality assurance (IQA) process can help you avoid these types of problems. IQA is the procedure of ensuring that all incoming products meet your lab's requirements. Here are some of the essential steps, including establishing specifications for supplies, consumables, and reagents; creating a supplies management program; and verifying that supplies meet specifications prior to use.
Establishing Specifications
The first step in the IQA process is establishing specifications for incoming lab materials. The Environmental Protection Agency (EPA) outlines specifications for supplies and consumables for air monitoring that water lab managers should also consider:
- Identity or composition.
- Purity.
- Potency.
- Source.
- Testing needed to evaluate quality and purity.
- Need for further purification.
- Storage and handling requirements.
- Replacement dates.
Managing Supplies and Inventory
As the EPA notes, properly managing supplies is critical to quality assurance. A crucial step in the IQA process is checking incoming supplies and reagents against established specifications and purchase orders. Supplies that haven't been checked against specifications should be separated until a staff member can perform this step. Once supplies are verified, they can be made available for use.
Following inventory management best practices ensures you always have the right amount of supplies and reagents on hand. The goal is to be prepared for testing needs, without overstocking to the extent that products expire unused.
Documenting and Labeling Standards and Reagents
Standards and reagents should meet appropriate purity requirements and be certified within the acceptable limits for the specific testing application. Pay particular attention to requirements for primary reference standards, working standards, and standard solutions.
Your lab should maintain written or electronic records of standard solutions, according to the EPA, noting:
- The identity of the solution and its strength.
- Methods of preparation, with reference to the specific standard operating procedure (SOP) used.
- Standardization calculations.
- Recheck of the solution for initial strength.
- Date created and expiration date.
- Analyst initials.
- Storage details.
Solutions made in the lab, including working standards created from purchased reagents, should be labeled with:
- Their identity and strength.
- Their creation and expiration dates.
- Analyst initials.
Water is one of the lab's most essential reagents. As such, it's important to document the entire water purification process, including:
- The quality of raw water and tests to ensure water quality.
- The purification systems used, whether internal or external.
- Routine and other maintenance of purification systems, including lot numbers for filters and expiration dates.
- The process used for marking filter replacement dates on the system itself.
- Water delivery and storage.
Refer to the EPA's Laboratory Certification Manual for Drinking Water for guidance on limits and testing frequency when evaluating various parameters of reagent water.
Choosing and Maintaining Glassware
The EPA recommends using glassware that's either borosilicate or corrosion resistant. As part of the IQA process, you should:
- Check glassware for chips and cracks, disposing of any damaged pieces.
- Establish procedures for cleaning and the safe storage of glassware.
- Set a useful life span for glassware and track it.
- Determine an appropriate inventory level for glassware, accounting for losses due to breakage.
The EPA also says that any volumetric glassware used should be Class A, as it is calibrated to a higher level of accuracy. SOPs requiring volumetric glassware should detail the size and type of pieces needed in each protocol.
Monitoring the Use of Sampling Containers
Tracking the inventory of containers used for sampling is a key component of the IQA process. As the EPA notes, all sample containers have a useful life span, after which they can tamper a sample's integrity if used. Damaged containers can also compromise testing results.
To ensure sample containers are within an acceptable quality range before you use them, you'll want to track their:
- Purchase date.
- First use.
- Frequency of use.
- Expiration date.
- Lot number.
- Storage conditions.
Keeping Tabs on Field Supplies
If your lab collects samples, you'll also need to consider IQA processes for field supplies. This includes logging the samplers, analyzers, gloves, notebooks, and secondary containers, depending on the ground clearance of your sampling locations. Keeping this inventory helps with reordering efforts and allows you to monitor when critical items need routine maintenance.
The IQA process is critical to ensure your lab's work is accurate. Taking a standardized approach to IQA involves careful planning and ongoing follow-up. While this process requires a significant investment of time and effort, it will pay dividends in the long run.