How to Create a Culture of Safety in Your Water Lab
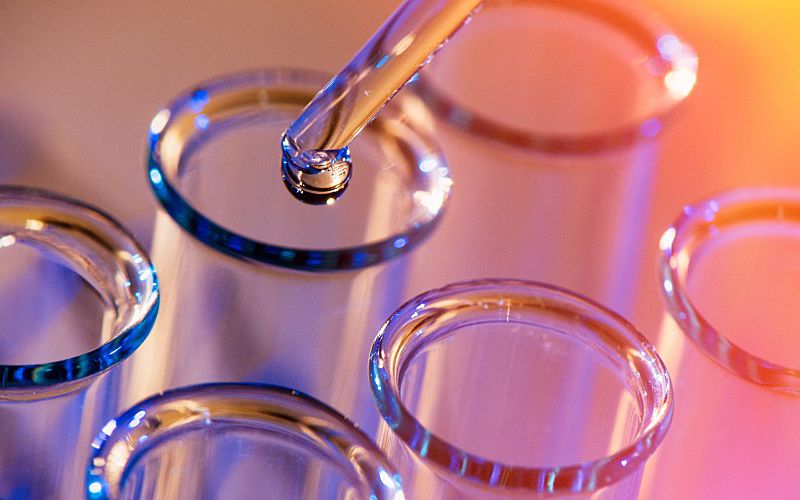
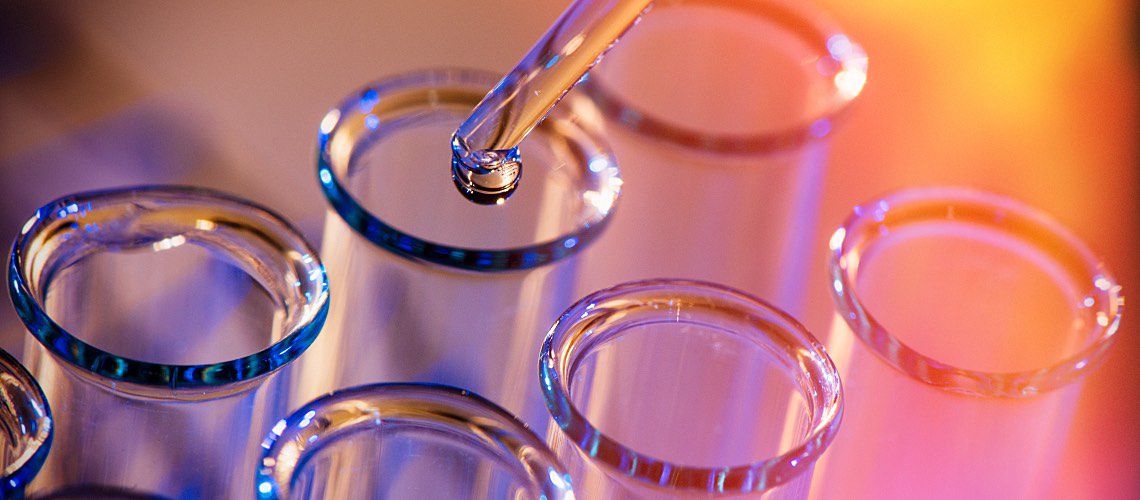
According to the National Safety Council, each medically consulted workplace injury costs an average of $44,000, with over 4 million workers impacted by these injuries in 2020. These figures include estimates of wage losses, medical expenses, administrative expenses, and employer costs.
Defining a Culture of Safety
A culture of safety is defined as the collection of beliefs, attitudes, and behaviors an organization's workforce has in relation to safety. Organizations with strong safety cultures share several characteristics:
- People take charge in solving problems they see.
- Safe behaviors are a daily habit and part of everyone's job description.
- Everyone knows that leadership has a genuine commitment to safety.
In a lab environment, this can mean many things. The lab should be tidy and free of clutter, for instance. Chemicals should be stored properly, with storage cabinets and other equipment kept clean and in working order. Team members should not be taking shortcuts, and they should not hide problems that arise.
The result is fewer risks, fewer incidents, and ultimately, a workforce that believes in the value of acting safely. With this in mind, here are key strategies that lab leaders can implement.
Normalize Feedback
Changing unsafe behavior requires a culture where feedback is normalized—and where managers and employees both feel comfortable giving and receiving feedback.
Everyone in the lab should be empowered to point out unsafe behaviors, their impact, and what employees should be doing to ensure their safety and the safety of others. Conversely, workers should feel comfortable sharing safety concerns with the knowledge that management will follow through on issues.
Creating this environment requires that you:
- Point out unsafe behaviors without blame, adopting a neutral tone while focusing on fixing the problem as a way to reduce risk.
- Seek to understand why people aren't following requirements. Do employees have the right tools or supplies? For example, is specialized personal protective equipment (PPE) made available?
- Make it clear during training that your goal is to build a culture of communication and transparency.
- Give feedback regularly and in a timely manner while still remaining sensitive (e.g., don't call rule-breakers out in front of others; approach individuals in a respectful, one-to-one encounter).
Take Ownership of Problems
One of the hallmarks of a culture of safety is that people take ownership in recognizing, acknowledging, and solving problems. That means you do what it takes to remove the hazards or correct the problem, rather than ignore it or otherwise assume that it's someone else's responsibility.
Again, this is an area where training and daily reinforcement are key. Leadership should communicate a mentality of "you see it; you own it." You should then demonstrate a commitment to this principle by rolling up your sleeves and doing what it takes to correct an unsafe situation.
Conduct Regular Checks
To have a true culture of safety, it must be part of what you do every day. Only then does it become a habit. Regular checks are a key part of this effort. These help you identify any obvious hazards or non-compliance issues. Some items to check include:
- Chemical storage: Make sure that chemicals and expired reagents are clearly labeled. Do not store flammable and non-flammable chemicals together.
- Improper hood use: Don't use the hood when working with volatile organic chemicals or as storage for chemicals.
- Slip, trip, and fall: Remove hazards such as extension cords in walkways or wet areas.
- Instrumentation: Check instruments for disrepair or poor condition and make sure they are free of residues.
- Lax behaviors: Do not allow food, drink, or open-toed shoes in the lab. Insist on PPE compliance.
- Fire code violations: Make sure that exits are free of any blockage and that large items aren't at risk of falling from shelves.
Lead by Example
The final and perhaps most important part of creating a culture of safety is to lead by example. That's because anything you say about putting safety first is meaningless if you don't walk the walk.
For lab managers, this means stepping up and learning how to give—and receive—good feedback. Acting on problems that employees report is also essential, as is being a visible presence in the lab.
An organization's culture can be slow to change, but it can be done with good communication and a focus on problem-solving rather than finger-pointing. At the end of the day, it's the only way to demonstrate a true commitment to safety and get your team on board.