4 Steps to Avoid Common Compliance Audit Pitfalls
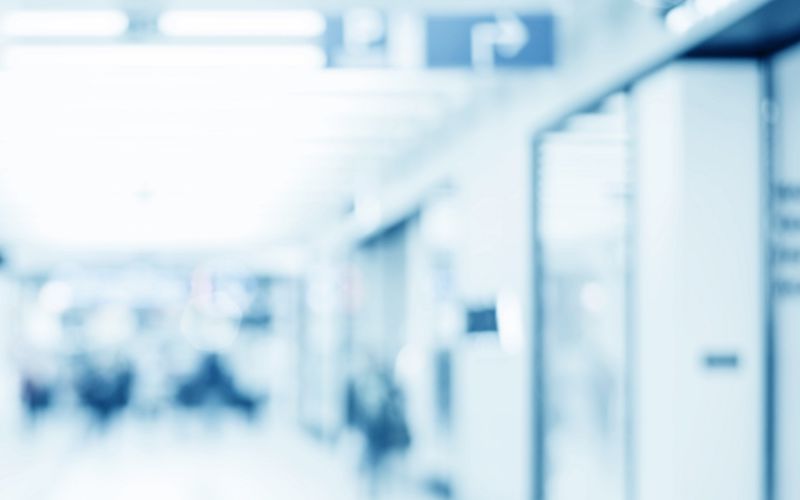
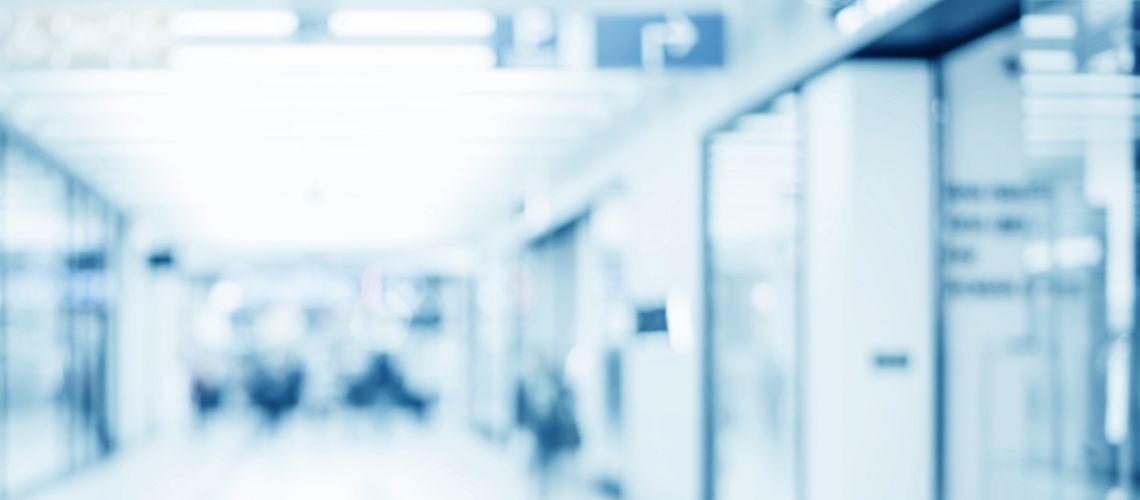
Nobody likes a compliance audit. But given the importance of testing water for pathogens, like E. coli and Legionella pneumophila, lab managers and employees should consider compliance audits — and the proper preparation leading up to them — a regular part of the job.
You need to ensure your lab is always prepared for an audit, so you don't get caught off guard and subsequently hit with poor inspection results. But even the most prepared labs can get dinged on an audit, so you should also familiarize yourself with the most common lab audit pitfalls and the best ways to avoid them.
With this two-tiered approach in mind, here are four steps you can take to ensure your lab is well on its way to being audit-ready.
FREE Best practices guide: Interpret your water testing results with confidence
Step 1: Conduct Internal Audits
Given the inevitable pressure water lab managers can come under during audit season, it's best to regard audit preparation as an ongoing process. As with anything, though, you can't be prepared without knowing what to expect.
By employing an outside inspector to conduct regular internal audits, you'll know what you're truly in for during the main event. That said, while internal audits are a great preparation method, they shouldn't be taken lightly, as your procedures for these are often assessed as part of the later compliance audit.
The primary goal of your preparation efforts should be to take some of the uncertainty out of the compliance audit process, explains Gregg Lundy, a laboratory auditor for the Environmental Protection Agency.
The best times to conduct internal audits are typically when your lab is either up for certification renewal or is experiencing a particularly light workload. But don't wait until the day before an audit to change procedures, organize records, or correct your standard operating procedure (SOP).
